Zero Defects (or ZD) was a management-led program to eliminate defects in industrial production that enjoyed brief popularity in American industry from 1964 to the early 1970s. Quality expert
Philip Crosby later incorporated it into his "Absolutes of Quality Management" and it enjoyed a renaissance in the American automobile industry—as a performance goal more than as a program—in the 1990s. Although applicable to any type of enterprise, it has been primarily adopted within
supply chain
A supply chain is a complex logistics system that consists of facilities that convert raw materials into finished products and distribute them to end consumers or end customers, while supply chain management deals with the flow of goods in distri ...
s wherever large volumes of components are being purchased (common items such as nuts and bolts are good examples).
Definition
" ..Zero Defects is a management tool aimed at the reduction of defects through prevention. It is directed at motivating people to prevent mistakes by developing a constant, conscious desire to do their job right the first time." — ''Zero Defects: A New Dimension in Quality Assurance''
Zero Defects seeks to directly reverse the attitude that the number of mistakes a worker makes doesn't matter since inspectors will catch them before they reach the customer.
This stands in contrast to activities that affect the worker directly, such as receiving a paycheck in the correct amount. Zero Defects involves
reconditioning the worker "to take a personal interest in everything he does
by convincing him that his job is just as important as the task of the doctor or the dentist."
History
The development of Zero Defects is credited to
Philip B. Crosby, a quality control department manager on the
Pershing missile program at the
Martin Company,
though at least one contemporary reference credits a small, unnamed group of Martin employees.
Zero Defects was not the first application of motivational techniques to production: during World War II, the
War Department's "E for Excellence" program sought to boost production and minimize waste.
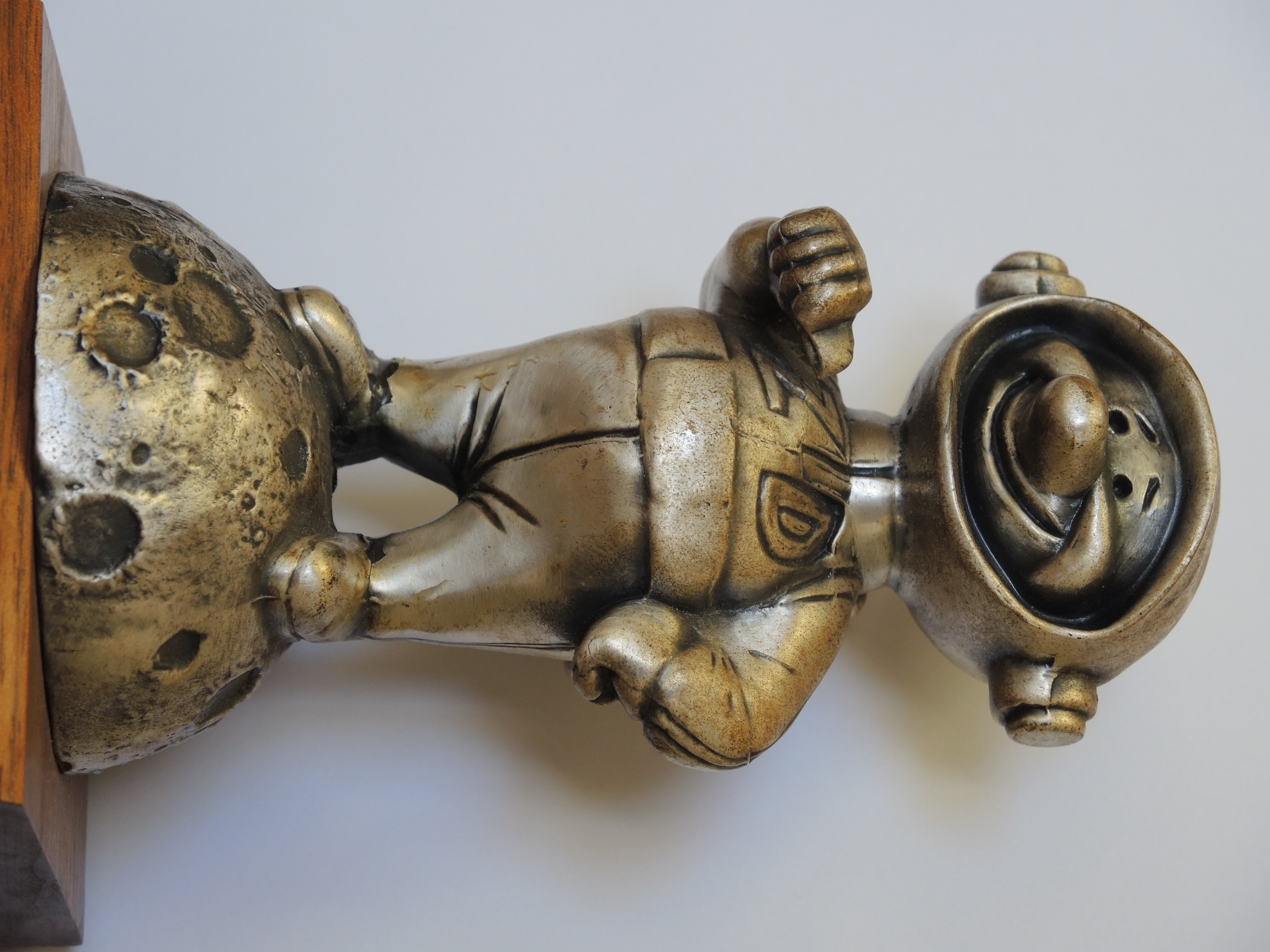
The
Cold War
The Cold War was a period of global Geopolitics, geopolitical rivalry between the United States (US) and the Soviet Union (USSR) and their respective allies, the capitalist Western Bloc and communist Eastern Bloc, which lasted from 1947 unt ...
resulted in increased spending on the development of defense technology in the 1950s and 1960s. Because of the safety-critical nature of such technology, particularly weapons systems, the government and defense firms came to employ hundreds of thousands of people in inspection and monitoring of highly-complex products assembled from hundreds of thousands of individual parts.
This activity routinely uncovered defects in design, manufacture, and assembly and resulted in an expensive, drawn out cycle of inspection, rework, reinspection, and retest.
Additionally, reports of spectacular missile failures appearing in the press heightened the pressure to eliminate defects.
In 1961, the Martin Company's Orlando Florida facility embarked on an effort to increase quality awareness and specifically launched a program to drive down the number of defects in the Pershing missile to one half of the
acceptable quality level in half a year's time.
Subsequently, the Army asked that the missile be delivered a month earlier than the contract date in 1962. Martin marshaled all of its resources to meet this challenge and delivered the system with no discrepancies in hardware and documentation and were able to demonstrate operation within a day of the start of setup.
After reviewing how Martin was able to overachieve, its management came to the conclusion that while it had not insisted on perfection in the past, it had in this instance, and that was all that was needed to attain outstanding product quality.
Management commissioned a team to examine the phenomenon and come up with an action plan, which became the organizing, motivating, and initiating elements of Zero Defects.
The
Department of Defense
The United States Department of Defense (DoD, USDOD, or DOD) is an executive department of the U.S. federal government charged with coordinating and supervising the six U.S. armed services: the Army, Navy, Marines, Air Force, Space Force, ...
also took notice and in 1964, began to actively encourage its vendors to adopt Zero Defects programs. Interest in the program from outside firms, including
Litton Industries,
Thiokol
Thiokol was an American corporation concerned initially with rubber and related chemicals, and later with rocket and missile propulsion systems. Its name is a portmanteau of the Greek words for sulfur () and glue (), an allusion to the company ...
,
Westinghouse, and
Bendix Corporation,
was keen and many made visits to Martin to learn about it.
Their feedback was incorporated and rounded out the program. In particular,
General Electric
General Electric Company (GE) was an American Multinational corporation, multinational Conglomerate (company), conglomerate founded in 1892, incorporated in the New York (state), state of New York and headquartered in Boston.
Over the year ...
suggested that error cause removal be included in the program.
Martin claimed a 54% defect reduction in defects in hardware under government audit during the first two years of the program. General Electric reported a $2 million reduction in rework and scrap costs,
RCA reported 75% of its departments in one division were achieving Zero Defects, and
Sperry Corporation
Sperry Corporation was a major American equipment and electronics company whose existence spanned more than seven decades of the 20th century. Sperry ceased to exist in 1986 following a prolonged hostile takeover bid engineered by Burroughs ...
reported a 54% defect reduction over a single year.
During its heyday, it was adopted by
General Electric
General Electric Company (GE) was an American Multinational corporation, multinational Conglomerate (company), conglomerate founded in 1892, incorporated in the New York (state), state of New York and headquartered in Boston.
Over the year ...
,
ITT Corporation
ITT Inc., formerly ITT Corporation, is an American worldwide manufacturing company based in Stamford, Connecticut. The company produces specialty components for the aerospace, transportation, energy and industrial markets. ITT's three businesses ...
,
Montgomery Ward
Montgomery Ward is the name of two successive U.S. retail corporations. The original Montgomery Ward & Co. was a mail-order business and later a department store chain that operated between 1872 and 2001; its common nickname was "Monkey Wards". ...
, the
United States Army
The United States Army (USA) is the primary Land warfare, land service branch of the United States Department of Defense. It is designated as the Army of the United States in the United States Constitution.Article II, section 2, clause 1 of th ...
among other organizations.
While Zero Defects began in the aerospace and defense industry, thirty years later it was regenerated in the automotive world. During the 1990s, large companies in the
automotive industry
The automotive industry comprises a wide range of company, companies and organizations involved in the design, Business development, development, manufacturing, marketing, selling, Maintenance, repairing, and Custom car, modification of motor ve ...
cut costs by reducing their quality inspection processes and demanding that their suppliers dramatically improve the quality of their supplies.
Later developments
In 1979, Crosby penned ''Quality Is Free: The Art of Making Quality Certain'' which preserved the idea of Zero Defects in a
Quality Management Maturity Grid, in a 14-step quality improvement program, and in the concept of the "Absolutes of Quality Management".
The quality improvement program incorporated ideas developed or popularized by others (for example,
cost of quality (step 4), employee education (step 8), and
quality councils (step 13)) with the core motivation techniques of booklets, films, posters, speeches, and the "ZD Day" centerpiece.
Absolutes of Quality Management
According to Crosby, there are four Absolutes:
1. "The definition of quality is conformance to requirements"
Newcomers to manufacturing bring their own vague impressions of what quality involves. But in order to tackle quality-related problems, there must be widespread agreement on the specifics of what quality means for a particular product. Customer needs and expectations must be reduced to measurable quantities like length, or smoothness, or roundness and a standard must be specified for each. These become the requirements for a product and the organization must inspect, or measure what comes out of the production process against those standards to determine whether the product conforms to those requirements or not.
An important implication of this is that if management does not specify these requirements workers invent their own which may not align with what management would have intended had they provided explicit requirements to begin with.
2. "The system of quality is prevention"
Companies typically focus on
inspection
An inspection is, most generally, an organized examination or formal evaluation exercise. In engineering activities inspection involves the measurements, tests, and gauges applied to certain characteristics in regard to an object or activity. ...
to ensure that defective product doesn't reach the customer. But this is both costly and still lets nonconformances through.
Prevention, in the form of "pledging ourselves to make a constant conscious effort to do our jobs right the first time", is the only way to guarantee zero defects. Beyond that, examining the production process for steps where defects can occur and
mistake proofing them contributes to defect-free production.
3. "The performance standard is Zero Defects"
Workers, at least during the
post–World War II economic expansion
The post–World War II economic expansion, also known as the postwar economic boom or the Golden Age of Capitalism, was a broad period of worldwide economic expansion beginning with the aftermath of World War II and ending with the 1973–1975 r ...
, had a lackadaisical attitude on the whole toward work. Crosby saw
statistical quality control and the MIL-Q-9858 standard as contributing to this through
acceptable quality levels—a concept that allows a certain number of acceptable defects and reinforces the attitude that mistakes are inevitable.
Another contributor is the self-imposed pressure to produce something to sell, even if that thing is defective.
Workers must "make the attitude of Zero Defects
heir
Inheritance is the practice of receiving private property, titles, debts, entitlements, privileges, rights, and obligations upon the death of an individual. The rules of inheritance differ among societies and have changed over time. Offi ...
personal standard."
4. "The measurement of quality is the price of nonconformance"
To convince executives to take action to resolve issues of poor quality, costs associated with poor quality must be measured in monetary terms.
Crosby uses the term "the price of nonconformance" in preference to "
the cost of quality" to overcome the misimpression that higher quality requires higher costs.
The point of writing ''Quality Is Free'' was to demonstrate that quality improvement efforts pay for themselves.
Crosby divides
quality-related costs into the price of conformance and the price of nonconformance. The price of conformance includes quality-related planning, inspection, and auditing; the price of nonconformance includes scrap, rework, claims against warranty, unplanned service
Criticisms
The main criticism is the amount of effort required to verify every person's performance in an organization.
Confidence in the program, and therefore compliance with it, fades without this verification.
Point 10 of
Deming's 14 points ("''Eliminate slogans, exhortations, and targets for the work force asking for ''zero defects'' and new levels of productivity.''") is clearly aimed at ZD.
Joseph M. Juran was also critical of ZD.
Another criticism is that Zero Defects is a motivational program aimed at encouraging employees to do better.
Crosby stated that "Motivation has nothing to do with it...It is merely setting performance standards that no one can misunderstand and then starting a two-way communications exercise to let everyone know about it."
He blamed management actions and attitudes for creating the opportunity for defects.
See also
*
Six Sigma
Six Sigma (6σ) is a set of techniques and tools for process improvement. It was introduced by American engineer Bill Smith while working at Motorola in 1986.
Six Sigma strategies seek to improve manufacturing quality by identifying and removin ...
*
Total Quality Management
Total quality management (TQM) is an organization-wide effort to "install and make a permanent climate where employees continuously improve their ability to provide on-demand products and services that customers will find of particular value." ...
Notes
References
Further reading
*
*
*
*
External links
Zero Defects at Lockheed Martin, the descendant of the Martin CompanyPhoto of Governor William W. Scranton of Pennsylvania speaking at a Zero Defects kickoff at Boeing Vertol in 1965
{{Authority control
1962 introductions
Business terms
Quality management