
Centrifugal pumps are used to transport fluids by the conversion of rotational kinetic energy to the hydrodynamic energy of the fluid flow. The rotational energy typically comes from an engine or electric motor. They are a sub-class of dynamic axisymmetric work-absorbing
turbomachinery
Turbomachinery, in mechanical engineering, describes machines that transfer energy between a rotor and a fluid, including both turbines and compressors. While a turbine transfers energy from a fluid to a rotor, a compressor transfers energy from ...
.
The fluid enters the pump impeller along or near to the rotating axis and is accelerated by the impeller, flowing radially outward into a diffuser or
volute
A volute is a spiral, scroll-like ornament that forms the basis of the Ionic order, found in the capital of the Ionic column. It was later incorporated into Corinthian order and Composite column capitals. Four are normally to be found on an Ion ...
chamber (casing), from which it exits.
Common uses include water, sewage, agriculture, petroleum, and petrochemical pumping. Centrifugal pumps are often chosen for their high flow rate capabilities, abrasive solution compatibility, mixing potential, as well as their relatively simple engineering. A
centrifugal fan is commonly used to implement an
air handling unit
An air handler, or air handling unit (often abbreviated to AHU), is a device used to regulate and circulate air as part of a heating, ventilating, and air-conditioning (HVAC) system. An air handler is usually a large metal box containing a blowe ...
or
vacuum cleaner. The reverse function of the centrifugal pump is a
water turbine
A water turbine is a rotary machine that converts kinetic energy and potential energy of water into mechanical work.
Water turbines were developed in the 19th century and were widely used for industrial power prior to electrical grids. Now, ...
converting potential energy of water pressure into mechanical rotational energy.
History
According to Reti, the first machine that could be characterized as a centrifugal pump was a mud lifting machine which appeared as early as 1475 in a treatise by the Italian Renaissance engineer
Francesco di Giorgio Martini
Francesco di Giorgio Martini (1439–1501) was an Italian architect, engineer, painter, sculptor, and writer. As a painter, he belonged to the Sienese School. He was considered a visionary architectural theorist—in Nikolaus Pevsner's terms ...
.
True centrifugal pumps were not developed until the late 17th century, when
Denis Papin
Denis Papin FRS (; 22 August 1647 – 26 August 1713) was a French physicist, mathematician and inventor, best known for his pioneering invention of the steam digester, the forerunner of the pressure cooker and of the steam engine.
Early ...
built one using straight vanes. The curved vane was introduced by British inventor
John Appold in 1851.
How it works

Like most pumps, a centrifugal pump converts rotational energy, often from a motor, to energy in a moving fluid. A portion of the energy goes into kinetic energy of the fluid. Fluid enters axially through eye of the casing, is caught up in the impeller blades, and is whirled tangentially and radially outward until it leaves through all circumferential parts of the impeller into the diffuser part of the casing. The fluid gains both velocity and pressure while passing through the impeller. The doughnut-shaped diffuser, or scroll, section of the casing decelerates the flow and further increases the pressure.
Description by Euler
A consequence of Newton's second law of mechanics is the conservation of the angular momentum (or the “moment of momentum”) which is of fundamental significance to all turbomachines. Accordingly, the change of the angular momentum is equal to the sum of the external moments. Angular momentums ρ×Q×r×cu at inlet and outlet, an external torque M and friction moments due to shear stresses Mτ are acting on an impeller or a diffuser.
Since no pressure forces are created on cylindrical surfaces in the circumferential direction, it is possible to write Eq. (1.10) as:
:::
(1.13)
Euler's pump equation
Based on Eq.(1.13) Euler developed the head pressure equation created by the impeller see Fig.2.2
:::
(1)
:::
(2)
In Eq. (2) the sum of 4 front element number call static pressure, the sum of last 2 element number call velocity pressure look carefully on the Fig 2.2 and the detail equation.
H
t theory head pressure ; g = between 9.78 and 9.82 m/s2 depending on latitude,
conventional standard value of exactly 9.80665 m/s2
barycentric gravitational acceleration
u
2=r
2.ω the peripheral circumferential velocity vector
u
1=r
1.ω the inlet circumferential velocity vector
ω=2π.n angular velocity
w
1 inlet relative velocity vector
w
2 outlet relative velocity vector
c
1 inlet absolute velocity vector
c
2 outlet absolute velocity vector
Velocity Triangle
The color triangle formed by velocity vector u,c,w called "velocity triangle". This rule was helpful to detail Eq.(1) become Eq.(2) and wide explained how the pump works.
Fig 2.3 (a) shows triangle velocity of forward curved vanes impeller ; Fig 2.3 (b) shows triangle velocity of radial straight vanes impeller. It illustrates rather clearly energy added to the flow (shown in vector c) inversely change upon flow rate Q (shown in vector c
m).
Efficiency factor
,
where:
:
is the mechanics input power required (W)
:
is the fluid density (kg/m
3)
:
is the standard acceleration of gravity (9.80665 m/s
2)
:
is the energy Head added to the flow (m)
:
is the flow rate (m
3/s)
:
is the efficiency of the pump plant as a decimal
The head added by the pump (
) is a sum of the static lift, the head loss due to friction and any losses due to valves or pipe bends all expressed in metres of fluid. Power is more commonly expressed as kilowatts (10
3 W, kW) or
horsepower
Horsepower (hp) is a unit of measurement of power, or the rate at which work is done, usually in reference to the output of engines or motors. There are many different standards and types of horsepower. Two common definitions used today are t ...
. The value for the pump efficiency,
, may be stated for the pump itself or as a combined efficiency of the pump and motor system.
Vertical centrifugal pumps
Vertical centrifugal pumps are also referred to as cantilever pumps. They utilize a unique shaft and bearing support configuration that allows the volute to hang in the sump while the bearings are outside the sump. This style of pump uses no
stuffing box
A stuffing box or gland package is an assembly which is used to house a gland seal. It is used to prevent leakage of fluid, such as water or steam, between sliding or turning parts of machine elements.
Components
A stuffing box of a sailing boat ...
to seal the shaft but instead utilizes a "throttle bushing". A common application for this style of pump is in a
parts washer
A parts washer is a piece of equipment used to remove contaminants or debris, such as dirt, grime, carbon, oil, grease, metal chips, cutting fluids, mold release agents, ink, paint, and corrosion from workpieces. Parts washers are used in new ...
.
Froth pumps
In the mineral industry, or in the extraction of oilsand,
froth
Foams are materials formed by trapping pockets of gas in a liquid or solid.
A bath sponge and the head on a glass of beer are examples of foams. In most foams, the volume of gas is large, with thin films of liquid or solid separating the r ...
is generated to separate the rich minerals or bitumen from the sand and clays. Froth contains air that tends to block conventional pumps and cause loss of prime. Over history, industry has developed different ways to deal with this problem. In the pulp and paper industry holes are drilled in the impeller. Air escapes to the back of the impeller and a special expeller discharges the air back to the suction tank. The impeller may also feature special small vanes between the primary vanes called split vanes or secondary vanes. Some pumps may feature a large eye, an inducer or recirculation of pressurized froth from the pump discharge back to the suction to break the bubbles.
Multistage centrifugal pumps
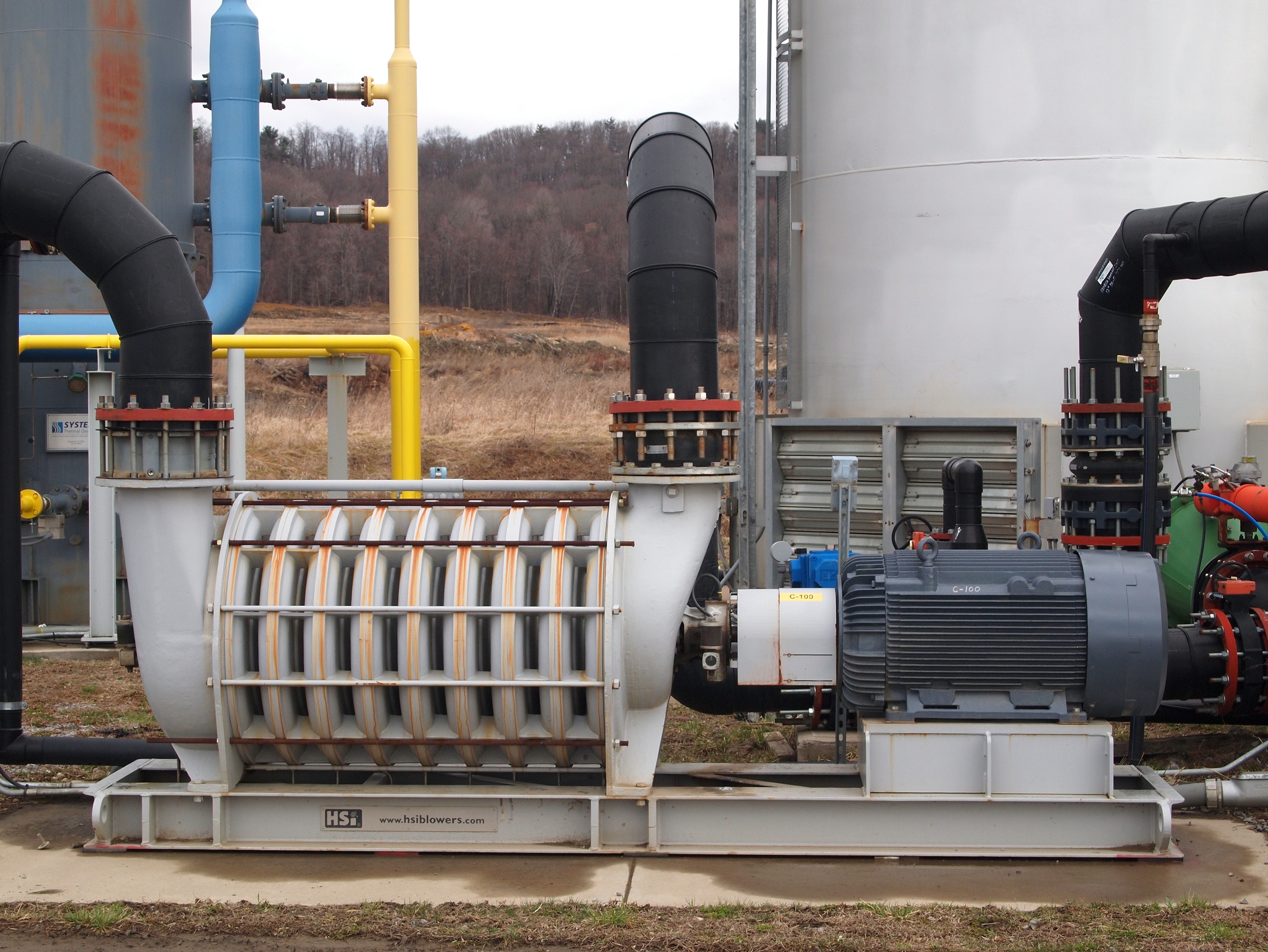
A centrifugal pump containing two or more impellers is called a multistage centrifugal pump. The impellers may be mounted on the same shaft or on different shafts. At each stage, the fluid is directed to the center before making its way to the discharge on the outer diameter.
For higher pressures at the outlet, impellers can be connected in series. For higher flow output, impellers can be connected in parallel.
A common application of the multistage centrifugal pump is the
boiler feedwater pump
A boiler feedwater pump is a specific type of pump used to pump feedwater into a steam boiler. The water may be freshly supplied or returning condensate produced as a result of the condensation of the steam produced by the boiler. These pumps are ...
. For example, a 350 MW unit would require two feedpumps in parallel. Each feedpump is a multistage centrifugal pump producing 150 L/s at 21 MPa.
All energy transferred to the fluid is derived from the mechanical energy driving the impeller. This can be measured at
isentropic
In thermodynamics, an isentropic process is an idealized thermodynamic process that is both adiabatic and reversible. The work transfers of the system are frictionless, and there is no net transfer of heat or matter. Such an idealized process ...
compression, resulting in a slight temperature increase (in addition to the pressure increase).
Energy usage
The energy usage in a pumping installation is determined by the flow required, the height lifted and the length and
friction characteristics of the pipeline.
The power required to drive a pump (
), is defined simply using SI units by:
:
where:
:
is the input power required (W)
:
is the fluid density (kg/m
3)
:
is the standard acceleration of gravity (9.80665 m/s
2)
:
is the energy Head added to the flow (m)
:
is the flow rate (m
3/s)
:
is the efficiency of the pump plant as a decimal
The head added by the pump (
) is a sum of the static lift, the head loss due to friction and any losses due to valves or pipe bends all expressed in metres of fluid. Power is more commonly expressed as kilowatts (10
3 W, kW) or horsepower (hp = kW/0.746). The value for the pump efficiency,
, may be stated for the pump itself or as a combined efficiency of the pump and motor system.
The energy usage is determined by multiplying the power requirement by the length of time the pump is operating.
Problems of centrifugal pumps
These are some difficulties faced in centrifugal pumps:
*
Cavitation—the net positive suction head (
NPSH
In a hydraulic circuit, net positive suction head (NPSH) may refer to one of two quantities in the analysis of cavitation:
# The Available NPSH (NPSH''A''): a measure of how close the fluid at a given point is to flashing, and so to cavitation. T ...
) of the system is too low for the selected pump
* Wear of the
impeller
An impeller or impellor is a rotor used to increase the pressure and flow of a fluid. It is the opposite of a turbine, which extracts energy from, and reduces the pressure of, a flowing fluid.
In pumps
An impeller is a rotating componen ...
—can be worsened by suspended solids or cavitation
*
Corrosion
Corrosion is a natural process that converts a refined metal into a more chemically stable oxide. It is the gradual deterioration of materials (usually a metal) by chemical or electrochemical reaction with their environment. Corrosion engi ...
inside the pump caused by the fluid properties
* Overheating due to low flow
* Leakage along rotating shaft.
*
Lack of prime—centrifugal pumps must be filled (with the fluid to be pumped) in order to operate
*
Surge
Surge means a sudden transient rush or flood, and may refer to:
Science
* Storm surge, the onshore gush of water associated with a low-pressure weather system
* Surge (glacier), a short-lived event where a glacier can move up to velocities 100 ...
*
Viscous liquids
In condensed matter physics and physical chemistry, the terms viscous liquid, supercooled liquid, and glassforming liquid are often used interchangeably to designate liquids that are at the same time highly viscous (see Viscosity of amorphous mater ...
may reduce efficiency
* Other pump types may be more suitable for high pressure applications
* Large solids or debris may clog the pump
Centrifugal pumps for solids control
An oilfield solids control system needs many centrifugal pumps to sit on or in mud tanks. The types of centrifugal pumps used are sand pumps, submersible slurry pumps, shear pumps, and charging pumps. They are defined for their different functions, but their working principle is the same.
Magnetically coupled pumps
Magnetically coupled pumps, or magnetic drive pumps, vary from the traditional pumping style, as the motor is coupled to the pump by magnetic means rather than by a direct mechanical shaft. The pump works via a drive magnet, 'driving' the pump rotor, which is magnetically coupled to the primary shaft driven by the motor. They are often used where leakage of the fluid pumped poses a great risk (e.g., aggressive fluid in the chemical or nuclear industry, or electric shock - garden fountains). They have no direct connection between the motor shaft and the impeller, so no stuffing box or
gland is needed. There is no risk of leakage, unless the casing is broken. Since the pump shaft is not supported by bearings outside the pump's
housing
Housing, or more generally, living spaces, refers to the construction and assigned usage of houses or buildings individually or collectively, for the purpose of shelter. Housing ensures that members of society have a place to live, whether i ...
, support inside the pump is provided by bushings. The pump size of a magnetic drive pumps can go from few watts of power to a giant 1 MW.
Priming
The process of filling the pump with liquid is called priming. All centrifugal pumps require liquid in the liquid casing to prime. If the pump casing becomes filled with vapors or gases, the pump impeller becomes gas-bound and incapable of pumping.
To ensure that a centrifugal pump remains primed and does not become gas-bound, most centrifugal pumps are located below the level of the source from which the pump is to take its suction. The same effect can be gained by supplying liquid to the pump suction under pressure supplied by another pump placed in the suction line.
Self-priming centrifugal pump
In normal conditions, common centrifugal pumps are unable to evacuate the air from an inlet line leading to a fluid level whose geodetic altitude is below that of the pump. Self-priming pumps have to be capable of evacuating air (see Venting) from the pump suction line without any external auxiliary devices.
Centrifugal pumps with an internal suction stage such as
water-jet pumps or side-channel pumps are also classified as self-priming pumps.
Self-Priming centrifugal pumps were invented in 1935. One of the first companies to market a self-priming centrifugal pump was
American Marsh in 1938.
Centrifugal pumps that are not designed with an internal or external self-priming stage can only start to pump the fluid after the pump has initially been primed with the fluid. Sturdier but slower, their impellers are designed to move liquid, which is far denser than air, leaving them unable to operate when air is present.
In addition, a suction-side swing
check valve or a vent valve must be fitted to prevent any
siphon action and ensure that the fluid remains in the casing when the pump has been stopped. In self-priming centrifugal pumps with a separation chamber the fluid pumped and the entrained air bubbles are pumped into the separation chamber by the impeller action.
The air escapes through the pump discharge nozzle whilst the fluid drops back down and is once more entrained by the impeller. The suction line is thus continuously evacuated. The design required for such a self-priming feature has an adverse effect on pump efficiency. Also, the dimensions of the separating chamber are relatively large. For these reasons this solution is only adopted for small pumps, e.g. garden pumps. More frequently used types of self-priming pumps are side-channel and water-ring pumps.
Another type of self-priming pump is a centrifugal pump with two casing chambers and an open impeller. This design is not only used for its self-priming capabilities but also for its degassing effects when pumping twophase mixtures (air/gas and liquid) for a short time in process engineering or when handling polluted fluids, for example, when draining water from construction pits.This pump type operates without a foot valve and without an evacuation device on the suction side. The pump has to be primed with the fluid to be handled prior to commissioning. Two-phase mixture is pumped until the suction line has been evacuated and the fluid level has been pushed into the front suction intake chamber by atmospheric pressure. During normal pumping operation this pump works like an ordinary centrifugal pump.
See also
*
Centrifugal compressor
Centrifugal compressors, sometimes called impeller compressors or radial compressors, are a sub-class of dynamic axisymmetric work-absorbing turbomachinery.
They achieve pressure rise by adding energy to the continuous flow of fluid through t ...
*
Axial flow pump
An axial-flow pump, or AFP, is a common type of pump that essentially consists of a propeller (an axial impeller) in a pipe. The propeller can be driven directly by a sealed motor in the pipe or by electric motor or petrol/diesel engines mounted ...
*
Net positive suction head (NPSH)
*
Pump
*
Seal (mechanical)
A mechanical seal is a device that helps join systems and mechanisms together by preventing leakage (e.g. in a pumping system), containing pressure, or excluding contamination. The effectiveness of a seal is dependent on adhesion in the case of ...
*
Specific speed
Specific speed ''N's'', is used to characterize turbomachinery speed.
Common commercial and industrial practices use dimensioned versions which are of equal utility. Specific speed is most commonly used in pump applications to define the su ...
(''N''
''s'' or ''N''
''ss'')
*
Thermodynamic pump testing
*
Turbine
A turbine ( or ) (from the Greek , ''tyrbē'', or Latin ''turbo'', meaning vortex) is a rotary mechanical device that extracts energy from a fluid flow and converts it into useful work. The work produced by a turbine can be used for generating ...
*
Turbopump
A turbopump is a propellant pump with two main components: a rotodynamic pump and a driving gas turbine, usually both mounted on the same shaft, or sometimes geared together. They were initially developed in Germany in the early 1940s. The purpo ...
Stainless Steel Centrifugal Pump
References
Sources
ASME B73 Standards Committee, Chemical Standard Pumps
External links
{{Authority control
Pumps
Gas compressors
Turbines
Hydraulic engineering
Power engineering
Articles containing video clips